
Steady State Operations
Typical wastes generated by metalworking businesses include solvents, degreasers, metal working fluids, lubricants, paint waste, wastewater pretreatment sludge, spent cleaners, grinding fines, swarf, shavings, and other metal waste that could be hazardous depending on adhering constituents, such as cooling fluids and lubricants deposited during the manufacturing process.
As an example, aqueous parts washers are commonly used in manufacturing or maintenance operations to remove grease, metal filings, tramp and cutting oils before performing finishing operations. Throughout this cleaning process, oils and solids will be deposited in the wash water containing the alkaline detergent as well as in the rinse water. Over time they will accumulate into a significant concentration reducing the efficiency of the cleaning process. Soon the water in a parts washer sump looks like the one shown in the inset of the picture on the right and becomes a liability that has to be handled properly in accordance with current statutes. Hazardous waste is subject to the Resource Conservation and Recovery Act (RCRA).
In conventional operations, the sump contents are periodically dumped to waste after one or two weeks of service. Typically this waste stream is hauled at rates
.png)
comparable to machine coolants. The emptied sump is refilled with fresh aqueous cleaner and a new cycle starts over again. The graph below shows the typical oil concentration as a function of time through this “remove and replace” cycle.
Although most parts washers have built-in filters and some may come with coalescers, they primarily remove solids with some tramp oils at best. This conventional technology is only partially effective because highly stabilized “oil-in-water” emulsion is created by the chemical reaction with detergents and cleaners (collectively called surfactants) used in parts washers. A constant agitation motion created in the washing process increases the emulsion even further. However, with more than twenty years’ experience in oily wastewater treatment, FSI has developed a most efficient and cost-effective filter to separate the emulsified oil from the water. The high efficiency filtration systems (WRS) provided by the company are commonly devised into processes to recycle oily wastewater to achieve a steady state
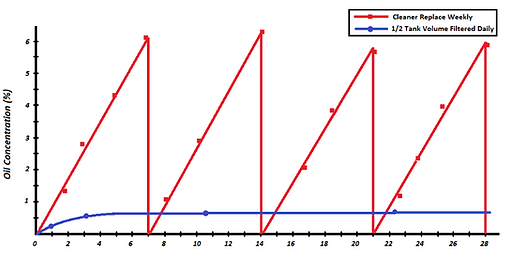.png)
Time (days)
operation, which turns a waste stream liability into an asset (see “steady state” curves on the graphs shown). An effective maintenance program will allow the alkaline washer cleaner to function more efficiently to provide longer service life of the alkaline cleaner. The key to a good maintenance program is to reach a Steady State process condition. This can be achieved through filtration as illustrated by the process diagram below; in which a working tank and a filtration system are incorporated into an oily wastewater (parts washer) sump as a bypass to form a closed loop. Part of the aqueous cleaner is regenerated through the filtration system by removing the oily and solids contaminants. A steady state is achieved in a closed-loop when the “oil-in” equals the “oil-out”. Under such a condition the oil concentration in the sump will maintain a low and constant threshold, this would improve productivity, minimize waste disposal and thus reduce the overall operating costs. The improved productivity includes product quality improvement, rework elimination and downtime reduction. The additional cost savings includes less replacement cleaner, less haul away expense, and fewer associated hazardous waste material compliance issues.
.png)
In the steady state operation, the final oil concentration level and the required time to reach equilibrium are dependent on the oil removal rate. As an example, Table 1 shows a system that reaches a steady state with a 50% daily oil removal rate. Notice that regardless of the starting oil level, whether a fresh sump with 0 ppm oil, as in Table 1(A), or a sump with 5,000 ppm oil, as in Table 1(B), the system will eventually reach a steady state.
.png)
The adjacent chart shows the oil concentration level at steady state for various oil removal rates. Apart from improving a parts washer application, the WRS and the setup of the steady state process are equally applicable to many other oily wastewater treatment applications; for example, the recycling of mop water from floor cleaning or the recycling of aqueous machine coolant, to cite a few.
Though it is possible to size a filtration system to achieve an oil free sump, the cost-benefit would be unfavorable for a short-term return-on-investment (ROI). However, rather than dwelling on an ideological goal, a practical approach for an achievable steady-state process can support a short-term ROI. This solution will also have a positive impact on a continuing ROI for managing oily wastewater. An effective filtration system minimizes a necessity for large sumps/tanks with excessive fluid-handling support equipment. FSI engineers can assist your specific separation application needs.
.png)