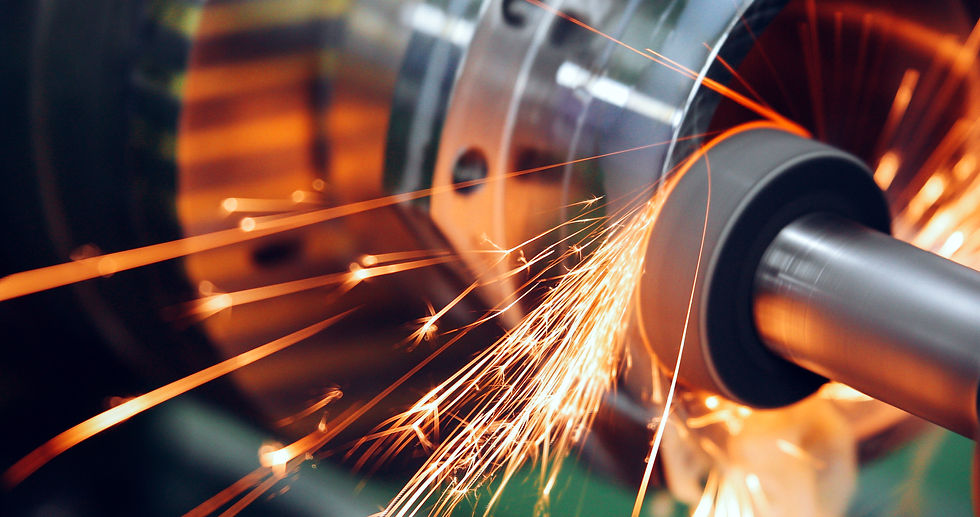
Metal Finishing Wastewater
Metal stocks from steel mills are coated with oils to protect the bare metal from corrosion or discoloration during handling, storage and shipping. During fabrication processes, coolants and lubricants are also applied to the metal working surface. Therefore, degreasing, which serves to remove mill oils, metal working fluids, and any other shop soils from the steel surface, is a necessary process to prepare for finishing in metal fabrication facilities. Degreasing is usually accomplished using nonionic surfactants in a heated and air-agitated bath. The surfactants surround the oil and dirt particles and form a stable emulsion that clean the parts and prevent the oil and dirt from redepositing on the metal surfaces.
For metal works that require painting, a pretreatment process is usually applied. Phosphating is a common type of pre-paint coating process used to simultaneously provide corrosion resistance and enhance paint adhesion to a metal surface. In many cases, a combined solution, such as a combination of Iron Phosphate and surfactant, is used for a cleaner/coater bath.
Aqueous cleaners, as a form of surfactant or a combined solution, have been used to replace solvent–based degreasers through the last two decades. Although they are a safe and effective alternative to solvent degreasers, they create large amounts of wastewater that are high in oil and grease concentration and potentially RCRA hazardous. A typical aqueous bath usually lasts from two to four months, when the buildup of oil in the tank begins to sacrifice product quality. Hauling away and replacing the spent cleaner results in a significant operation cost that reduces the bottom line profit. Driven by economic factors and advocacy by the US EPA and similar agencies at the state level, wastewater management through ultrafiltration (UF) has proven to be the most cost-effective technology and has been implemented by many metal working facilities for Cleaner Recycling through the years.
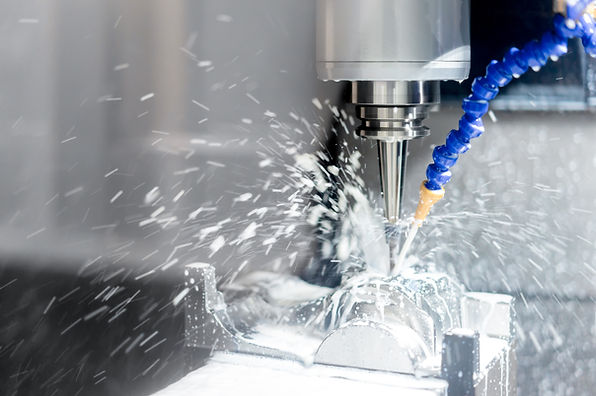
Ultrafiltration
Conventional filtration techniques rely on depth or screen filters to remove oil and dirt from a process solution. These filter media clog easily and their efficiency degrades over time. They have very limited service life or require frequent backwashing, which results in additional wastes. Membrane filtration is an advanced technique that takes advantage of thin film membranes and the shear force of cross-flow to achieve a more consistent process rate and a higher quality filtrate than conventional filtration. Ultrafiltration is one class of membrane filtration that uses membranes with pore diameters ranging from 0.01 to 0.1 micron (1 micron = 10-6 m). The ultrafiltration process works by producing two separate streams: concentrate (retentate) and permeate (filtrate). The permeate stream contains only the components in the feed solution small enough to pass through the membrane pores (water, solubilized ingredients). The concentrate stream contains everything else that is rejected by the membrane (emulsified oil and dirt). Highly emulsified oily wastewater is comprised of micron and submicron oil beads (most of the time coated by the surfactant) dispersed in water. Therefore, they can be effectively separated by UF.
To ensure long term effective service, the selection of a membrane to match a specific application is very important. Besides the selection of a pore size, other factors such as hydrophilicity, chemical compatibility, pH range, temperature range, clean ability, robustness, and cost are all important factors to be considered. There are many polymeric membranes available on the market. To name a few, a polyacrylonitrile (PAN) membrane is hydrophilic, which is usually preferred under aqueous environments to minimize fouling. A polyvinylidene difluoride (PVDF) is durable and has a wide operation range for pH and temperature. They all have their advantages and disadvantages. For each application, there is usually no best membrane but rather a most suitable membrane. Progress is constantly being made in membrane technology. There are new membranes with modified surface chemistry or engineered polymers that offer more benefits for many applications.
As a technology company, FSI has always maintained a portfolio of high quality membranes. Regardless of whether you are a new user or an experienced user looking for a UF system for your wastewater application, FSI will test your sample and come up with a system with the most suitable membrane for you. Often, it will pay off to replace systems that have been in operation for years, as they may no longer be commercially supported, or have been superseded by a more recent technology that is better suited for your specific application needs. For example, a ceramic membrane system was commonly used in the past to process alkaline cleaners from a hot bath because of high pH and high temperature (pH >12 @ 140°F). The ceramic membrane can be replaced by an engineered polymeric membrane today at less than half the cost. Additionally, the CAPEX and OPEX costs are significantly reduced due to a smaller horsepower pump being required in the system. This is because the modern polymeric membrane has a higher porosity and a thinner substrate resulting in a higher flux rate (permeate production rate per unit membrane area) and a lower energy consumption.