
Pilot Study
As a technology driven company, FSI's shop facility has the necessary, mechanical, electrical and control components, as well as data acquisition instruments, to perform testing according to various standardized test specifications. Also, the lab at FSI is oufitted with equipment that enables us to meet a wide range of test objectives ranging from conducting experiments to meeting various process fluid specifications to qualification of various filter media.
Industrial wastewater is unique to its originating process that is employed in a facility. The process can produce a wide variation in pollutant composition, particularly if it is subject to changes in components or operating conditions. Each case of industrial wastewater therefore requires a treatment that is specific to the constituents in that wastewater. Therefore, pilot testing is the only method of predicting performance to ensure a reliable complete system design.
Pilot trials usually involve a small unit with one or two membrane modules in the system. It is essential to have a representative wastewater sample or continuous access to the wastewater source on site. Too small a sample may not reveal significant variations in wastewater composition. Also, there are several key parameters that control the performance of membrane filtration:
1. Membrane pore size — Contrary to perception, a larger pore size does not necessarily indicate a higher flux rate in MF and UF. This is because those large pores facilitate penetration of small particles inside the pores to promote internal clogging. In addition, membrane porosity (pores per unit surface area) often increases as pore size rating becomes smaller.
2. Cross Flow Velocity — The velocity is in proportion to surface shear, which controls the thickness of the deposit layer on the membrane surface. With a low velocity, a dense cake can form on the membrane surface causing low permeate flow and plugging. In the extreme case with a zero velocity, a dead-end filtration is formed. This can plug a membrane in short time processing high solids-loading wastewater.
3. Transmembrane Pressure (TMP) — This is the difference between the driving pressure (average of the feed inlet and outlet pressure) and the permeate pressure. Higher TMP produces higher flux in general.
4. Composition of Feed — The characteristics of foulants have great effect on their propensity to adsorb to the membrane surface. They also dictate the chemicals (such as, caustic, acidic, oxidant) required for effective membrane cleaning. Other factors such as the concentration of suspended solids and fluid viscosity all have effects on filtration performance.
A well-planned pilot program will provide essential system design data with a high degree of confidence regarding:
1. The average permeate flow rate per unit membrane area (flux) and hence the membrane area required for a full-scale capacity.
2. Power required for a full-scale system.
3. Confirmation of permeate water quality to meet discharge or recycling requirements.
4. Confirmation of pretreatment chemistry formulations, residence times and effectiveness.
5. Determination of the required back pulse frequency.
6. A prediction of fouling rate to determine how often a clean in place (CIP) may need to be performed to remove foulants. (Note: This may only be reliable with large samples or continuous access to the waste water source.)
7. Chemical dosing quantities required and solids production rate.
FSI provides two types of pilot testing, Laboratory Pilot Testing and Field Pilot Testing as shown in the Table below.
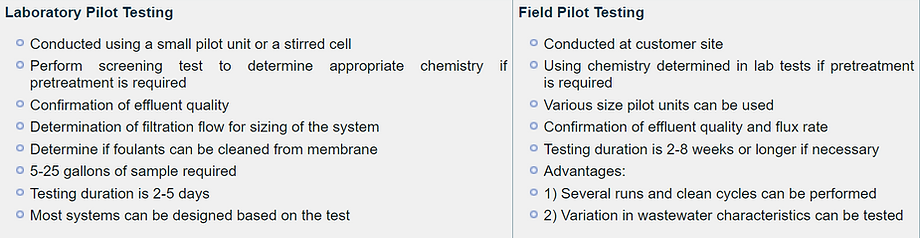.png)